Integrating Lean IT Principles into Industrial Operations
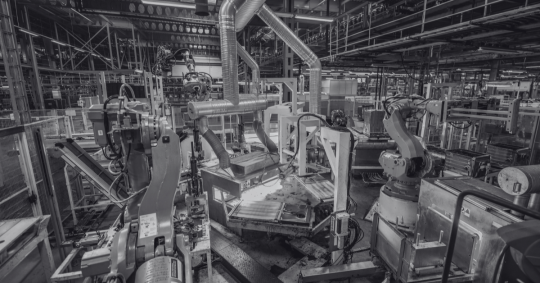
Integrating Lean IT principles into industrial operations can significantly enhance efficiency, reduce waste, and improve overall productivity. Lean IT, an adaptation of lean manufacturing principles, focuses on maximising value while minimising waste within information technology environments. By applying these principles to industrial settings, organisations can streamline processes, optimise resource utilisation, and achieve better outcomes.
Understanding Lean IT Principles
Lean IT is centred around several key principles:
- Value Streams: Identifying and understanding the flow of value to the customer is crucial. In IT, value streams represent the services provided to various stakeholders, including customers, suppliers, and employees. These services are categorised into primary (business services) and secondary (IT services) value streams. The goal is to ensure that every process contributes value to the end product or service.
- Value-Stream Mapping: This involves diagramming and analysing services to identify each component process step. By doing so, organisations can pinpoint and eliminate steps that do not deliver value, thereby reducing waste.
- Flow: Ensuring a smooth and uninterrupted flow of processes is vital. In Lean IT, this means eliminating unevenness (mura) through just-in-time systems that are tightly integrated, reducing delays and bottlenecks.
- Pull/Demand System: Lean IT emphasises a pull system, where processes are initiated based on actual demand rather than forecasts. This approach minimises overproduction and excess inventory, aligning production closely with customer needs.
Applying Lean IT in Industrial Operations
Integrating Lean IT principles into industrial operations involves several strategic steps:
- Identify Value Streams: Begin by mapping out all the processes that contribute to delivering value to the customer. This includes both manufacturing processes and IT services that support production. Understanding these streams helps identify areas where waste occurs.
- Implement Value-Stream Mapping: Create detailed maps of current processes to visualise the flow of materials and information. This visualisation aids in identifying non-value-adding activities, redundancies, and inefficiencies that can be eliminated or improved.
- Enhance Process Flow: Focus on creating a seamless flow of operations by removing obstacles that cause delays. This might involve reorganising the production floor, improving communication channels, or adopting technologies that facilitate real-time data sharing.
- Adopt a Pull System: Shift from a push-based production system to a pull-based one, where production is driven by actual customer demand. This approach reduces overproduction, minimises inventory costs, and ensures that resources are utilised effectively.
Benefits of Lean IT Integration
The integration of Lean IT principles into industrial operations offers numerous benefits:
- Reduced Waste: By identifying and eliminating non-value-adding activities, organisations can significantly reduce waste, leading to cost savings and more efficient operations.
- Improved Efficiency: Streamlined processes result in faster production times and better resource utilisation, enhancing overall operational efficiency.
- Enhanced Quality: With a focus on continuous improvement and error reduction, Lean IT helps in delivering higher-quality products and services.
- Increased Agility: Organisations become more responsive to market changes and customer demands, allowing for quicker adaptation and innovation.
Case Studies and Real-World Applications
Several organisations have successfully integrated Lean IT principles into their industrial operations:
Process Learning Factory CiP at TU Darmstadt
Established in 2007, this facility focuses on developing competencies for lean production and Industry 4.0. It simulates various industrial processes, allowing learners to apply lean methods and solve problems based on real-world scenarios.
Pilot Factory at TU Wien
This factory serves as a realistic test environment with real machines and production chains. It integrates various Industry 4.0 concepts, such as process adaptivity and human-machine interaction, demonstrating the practical application of Lean IT principles.
Stellenbosch Learning Factory
Located at Stellenbosch University, this facility provides training for lean operations and serves as a research platform for Industry 4.0. It integrates technologies like RFID tracking and real-time KPI visualisation to enhance learning and operational efficiency.
Challenges and Considerations
While the benefits are substantial, integrating Lean IT into industrial operations comes with challenges:
- Cultural Resistance: Employees accustomed to traditional workflows may resist changes. It's essential to encourage a culture that embraces continuous improvement and values employee input.
- Initial Investment: Implementing Lean IT may require upfront investments in technology and training. However, the long-term gains often justify these initial costs.
- Continuous Commitment: Lean is not a one-time project but an ongoing commitment. Organisations must be prepared to continually assess and refine their processes.
Conclusion
Integrating Lean IT principles into industrial operations is a transformative approach that aligns technology with lean methodologies to drive efficiency and value. By focusing on value streams, enhancing process flow, and adopting pull systems, organisations can reduce waste, improve quality, and respond more effectively to customer demands. While challenges exist, the successful applications in various learning factories and industrial settings demonstrate the potential of Lean IT to revolutionise industrial operations.