Keeping Industry Running Smoothly: Diagnosing and Solving Common Power Transmission Problems
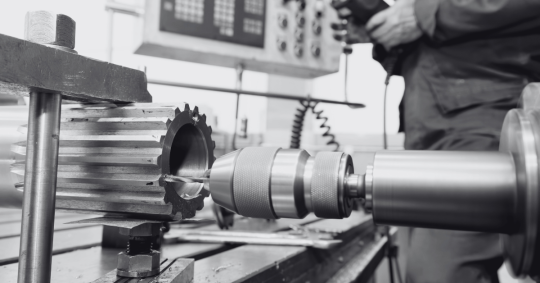
Industrial operations rely heavily on the seamless transfer of power from the source to the machinery performing the work. This intricate network of components, collectively known as the power transmission system, is the backbone of productivity. However, like any complex system, it's susceptible to issues that can lead to costly downtime, reduced efficiency, and even safety hazards.
Understanding common power transmission problems, their diagnosis and effective solutions is crucial for plant managers, maintenance engineers, and anyone involved in keeping industrial processes running smoothly.
The Perils of Misalignment
One of the most frequently encountered issues revolves around misalignment. Whether it's between shafts connected by couplings, pulleys on a belt drive, or gears in a gearbox, misalignment introduces undue stress on components. This can manifest as excessive vibration, premature wear on bearings and seals, increased noise levels, and even coupling or shaft failure.
Diagnosis: Diagnosing misalignment often involves visual inspection for obvious signs, but precise alignment requires tools like laser alignment systems or dial indicators.
Solutions: Solutions range from simple adjustments to the positioning of machinery to the replacement of damaged or worn flexible couplings designed to accommodate minor misalignments.
Tackling Troublesome Belt Drives
Belt drive problems are also common in many industrial settings. Issues can arise from improper belt tension, worn or damaged belts, misaligned pulleys, or environmental factors like dust and debris. Symptoms include belt slippage (leading to reduced power transfer and speed variations), excessive belt wear (cracking, fraying, or stretching), and squealing noises.
Diagnosis: Diagnosis involves checking belt tension with a tension gauge, visually inspecting belts for damage, and using a straight edge to ensure pulley alignment. Educational resources on industrial belt maintenance can also help you to diagnose these.
Solutions: Solutions include adjusting belt tension, replacing worn belts with the correct type and size, cleaning pulleys and the surrounding environment, and ensuring proper pulley alignment. Information on belt drive troubleshooting is often provided by industrial maintenance publications.
Understanding Gearbox Nightmares
Gearbox malfunctions can be particularly disruptive due to the critical role gearboxes play in altering speed and torque. Common problems include lubrication issues (too little, too much, or the wrong type of lubricant), worn or damaged gears (pitting, spalling, or breakage), bearing failure, and seal leaks. Unusual noises (grinding, whining, or clicking), excessive heat generation, and vibration are telltale signs.
Diagnosis: Diagnosis often requires careful listening, temperature monitoring, and potentially oil analysis to check for contaminants or wear particles. Understanding common gearbox failure modes is also crucial.
Solutions: Solutions can range from changing the lubricant and replacing seals to more complex repairs or complete gearbox replacement. The importance of proper industrial lubrication practices is highlighted by organisations like the Society of Tribologists and Lubrication Engineers (STLE).
Addressing Bearing Issues
Bearing failures are another significant cause of downtime in industrial machinery. Bearings support rotating shafts and reduce friction, but they are subject to wear and tear due to factors like overloading, improper lubrication, contamination, and misalignment. Symptoms of bearing failure can include increased noise (rumbling or clicking), excessive heat, vibration, and eventual seizure of the rotating component.
Diagnosis: Diagnosis often involves listening to the bearing with a stethoscope or using vibration analysis equipment. Educational materials on bearing failure analysis can be found on engineering education websites and materials science resources.
Solutions: Solutions invariably involve replacing the damaged bearing with the correct type and size, ensuring proper lubrication, and addressing the root cause of the failure (e.g., misalignment or overloading). Best practices for bearing maintenance are often covered in industrial maintenance training programs and materials.
Confronting Coupling Complications
Finally, coupling failures can occur due to misalignment, overloading, or wear and tear. Couplings connect driving and driven shafts, accommodating some degree of misalignment and transmitting power. Signs of failure include excessive vibration, noise, and eventual breakage of the coupling elements.
Diagnosis: Diagnosis involves visual inspection for damage and checking for proper alignment. Understanding the different types and applications of industrial couplings can be found in general mechanical engineering textbooks and online resources.
Solutions: Solutions involve replacing the damaged coupling with one suitable for the application and addressing any underlying misalignment issues. Information on selecting the appropriate coupling for specific industrial needs can be found in engineering design guides and materials.
Conclusion
Effective troubleshooting of power transmission issues relies on a combination of proactive maintenance practices, keen observation, and the use of appropriate diagnostic tools. Implementing regular inspection schedules, adhering to lubrication guidelines, ensuring proper alignment, and promptly addressing any unusual signs can significantly reduce the likelihood of major failures and keep industrial operations running smoothly and efficiently.
By understanding the common culprits and their remedies, businesses can minimise downtime, optimise performance, and ensure the longevity of their critical machinery.