The Role of Predictive Maintenance in Modern Manufacturing
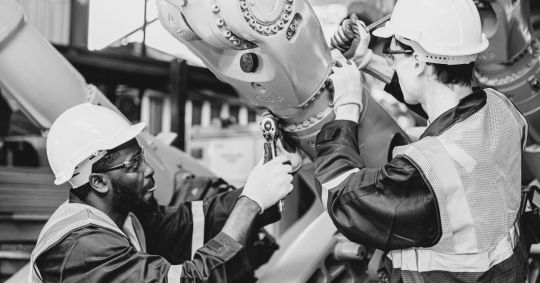
Manufacturing depends on machines running smoothly. When a machine breaks down, production stops, causing delays and high costs. Traditional maintenance methods often involve fixing equipment after it fails or performing routine maintenance, whether it is needed or not.
Predictive maintenance is a smarter approach. It uses technology to monitor machines in real time. This helps detect problems early and prevents breakdowns. Businesses can save time, reduce costs, and improve efficiency by keeping their equipment in top condition.
What Is Predictive Maintenance?
Predictive maintenance is a modern way to take care of machines. Instead of waiting for something to break, this method predicts when a failure might happen. It does this by using sensors, data, and artificial intelligence (AI).
By constantly tracking machine performance, businesses can plan repairs at the right time. This means less downtime, fewer unexpected failures, and longer-lasting equipment.
How Does Predictive Maintenance Work?
Predictive maintenance relies on technology to check machine health. Here’s how it works:
- Sensors collect data – Special sensors measure vibration, temperature, pressure, and other key factors.
- Data is analysed – The system looks for unusual patterns that could mean a problem is coming.
- Alerts are sent – If an issue is detected, the system notifies the maintenance team.
- Repairs are made in advance – Fixing small issues early prevents big breakdowns.
With this approach, businesses can avoid costly emergency repairs and keep machines running smoothly.
Key Benefits of Predictive Maintenance
1. Reduces Downtime
Unexpected machine failures can stop production completely. When a machine breaks down, it can take hours or even days to fix. This leads to lost time and missed deadlines.
Predictive maintenance helps avoid this. By detecting problems early, businesses can schedule repairs without stopping production. This keeps operations running and improves efficiency.
2. Lowers Maintenance Costs
Emergency repairs are expensive. When a machine suddenly stops working, it often needs urgent repairs, new parts, or even a full replacement.
Predictive maintenance helps prevent these costly situations. Fixing a small issue before it becomes a big problem saves money. It also reduces the need for frequent maintenance checks that may not be necessary.
3. Improves Workplace Safety
Faulty machines can be dangerous. A sudden failure could cause accidents, putting workers at risk.
By using predictive maintenance, businesses can identify potential risks before they lead to injuries. This helps create a safer work environment and prevents costly damage to machines.
4. Extends Equipment Lifespan
Machines that are well-maintained last longer. Wear and tear are normal, but when left unchecked, they can cause major failures.
Predictive maintenance helps slow down this process. By taking care of small issues early, equipment stays in good condition for longer. This reduces the need for frequent replacements and lowers overall costs.
5. Boosts Productivity
When machines stop working, production slows down or stops completely. This affects deadlines and can result in unhappy customers.
With predictive maintenance, businesses can plan maintenance without affecting daily operations. This ensures that production continues without unexpected disruptions.
The Role of IoT and Sensors in Predictive Maintenance
The Internet of Things (IoT) plays a key role in predictive maintenance. IoT connects machines to a central system, allowing real-time monitoring of equipment.
- Smart sensors detect problems early – These sensors track important factors like heat, vibration, and energy use.
- Wireless systems send instant alerts – If something is wrong, the system warns the maintenance team immediately.
- Cloud storage keeps data safe – Businesses can access reports anytime and make informed decisions.
By using IoT technology, businesses gain full visibility of machine health. This makes predictive maintenance more accurate and effective.
How to Implement Predictive Maintenance
Switching to predictive maintenance requires careful planning. Here are some steps businesses can take:
- Install Sensors on Machines – Sensors should be added to important equipment to monitor performance.
- Collect and Analyse Data – The software should track sensor readings and look for patterns.
- Set Up Automatic Alerts – Maintenance teams should receive notifications when an issue is detected.
- Schedule Maintenance When Needed – Instead of following a fixed schedule, repairs should be done only when necessary.
- Train Staff on New Technology – Employees should know how to use predictive maintenance tools properly.
With the right setup, businesses can improve efficiency and reduce unexpected machine failures.
The Future of Predictive Maintenance
Predictive maintenance is becoming more advanced every year. AI, machine learning, and IoT continue to improve, making this system even more accurate.
In the future, businesses may rely entirely on automated maintenance planning. Machines will be able to self-diagnose problems and even request repairs without human input.
By investing in predictive maintenance today, companies can stay ahead of the competition. They will enjoy lower costs, fewer breakdowns, and better overall performance.
Final Thoughts
Predictive maintenance is changing the way manufacturers care for their machines. Instead of fixing problems after they happen, businesses can now prevent failures before they occur. By using IoT and sensor technology, manufacturers can track machine health in real time. This leads to reduced downtime, lower maintenance costs, and improved productivity. At Robert Cupitt, we understand the importance of keeping machines in top condition. We provide high-quality industrial solutions to help businesses maintain their equipment.
Contact us today to learn more about our products and services, or for more industry insight check out our knowledge base.